The Plan-Do-Check-Act-Standardize Process (PDCAS)
You've heard me talk in the previous chapters about the Plan-Do-Check-Act process, or in short PDCA, which is one of the basic and most important planning tools of Kaizen. However, Kaizen has yet another process in place called SDCA, aka Standardize - Do - Check - Act, that follows the PDCA process. While it works well in business, especially in factories, it does not work well in real life situations. So I mixed these up and simply called the process PDCAS, adding the Standardize element to the PDCA process.
Anything you start in your life should follow these steps: Plan - Do - Check - Act.
As the name tells us, we plan something, we act according to the plan, we check to see if the plan was efficient, what worked and what not, and then act again. You never stop this cycle unless it's working at its maximum efficiency.
The moment you've twitched the plan enough times and you feel like it's going great, you standardize it. Aka you decide to use the exact same process over and over again. Until it fails you again, in which case you restart the process.
Let's take for example washing dishes. Many of us have been using the same standard plastic sponge for some time now. You know, the half yellow, half green one. While we thought it was good for a while, we've realized it is not zero waste, so now we need to look for alternatives.
Where do you start? What do you do? How do you find the perfect alternative?
Plan
What type of tool do you need? What should this tool help you achieve?
Remember the objects in your house are your employees.
If you were to tell Human Resources what exactly you want the sponge employee to do for you, what would you tell them?
E.g. "- I want the sponge to be soft enough to not mold according to the dish's shape, but strong enough to break away the dirt from the surface of the dish.
- I also want it to be long-lasting, because it has to follow the zero way guidelines.
- It must not be plastic, but made of either natural, regenerating materials or long-lasting materials that are easily recyclable."
Do
You then interview a few possible employees (aka do your research): the wool sponge, the loofah, the bokashi sponge and a bokashi sponge with a wooden handle, by testing them for a while, see which one can do the job the best.
Check
Are you happy with each of the alternative's results? Which one checks the most boxes? You pick one of them. For this example let's pick the bokashi sponge with a wooden handle.
Act
You use that new product for a while. It works great. You are satisfied with it. You decide this is your go-to product.
Standardize
Each time you need to wash dishes, you make sure the sponge is at an arm's reach. Decide where it will always stay. You make sure you are maintaining the sponge properly to be able to use it for a long time.
Congratulations! You've successfully accomplished the PDCAS cycle.
You have to realize that the process in itself, though sounds like a no-brainer, it will always be chaotic and stressful at first, but it will get better with each day. As long as you understand that the process will be unstable at first and you keep doing it until you get the hang of it, you will be alright.
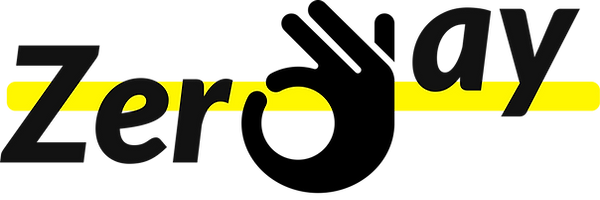
Abnormalities
Each time an abnormality occurs in a process that you've already standardized, you must ask yourself the below questions and start the PDCAS cycle again:
-> Was it because the product was not adequately chosen?
-> Was it because the process not good?
-> Or because the process was not followed?
-> Was it poor maintenance?
-> Why did this happen?
In our example:
>> these things might go wrong -> reason.
>> handle broke -> product wasn't adequate.
>> dishes weren't clean enough -> scrubbing time wasn't long enough, water too cold
>> dishes piled up in the sink -> process wasn't followed
>> sponge gathered mold -> sponge wasn't cleaned and set back to its original place
>> Why did it happen? No time, sponge too soft, bad design, hand hurts etc.
I know it's a bit overwhelming if you think you'd had to go through all of this thinking process for each and every object around your household, but fear not!!! If you repeat the process a few times, it will gradually become so easy and natural, it will take you less and less energy to do.
It's important to take it easy at first and do it slowly, with little pressure on yourself.
Perseverance is key.
Next, we need to talk about the importance of types of Value and prioritization.
But first, what is your opinion on the topic?
Do you think, to some extent, you have already been doing this process in your life?
Around the house or at the office?
Leave us a comment and let us know!